Nordrhein-Westfalen 2015
Exkursionsbericht zur Fachexkursion vom 26.05.2015 – 28.05.2015
Vom 26. bis 28. Mai 2015 führte das Institut für Bergbau, Abteilung für Maschinelle Betriebsmittel und Verfahren im Bergbau unter Tage, eine Fachexkursion in die traditionelle Bergbaubundesland Nordrhein-Westfalen zum Thema Bergbau unter Tage durch. Hierbei bot sich für die Studierende die Möglichkeit, die in theoretischen Lehrveranstaltungen und Praktika erworbenen Kenntnisse zu erweitern, zu vertiefen und einen Bezug zur Wirtschaft herzustellen. Außerdem bot sich durch den direkten Kontakt zu den Betrieben bzw. Unternehmen in diesem Zusammenhang den Studierenden ebenfalls die Möglichkeit zum „Networking“, sodass für Praktika sowie Fach- und Abschlussarbeiten erste Kontaktstellen hergestellt werden konnten.
An der dreitägigen Fachexkursion nahmen zwölf Studierende der Fachrichtungen Energie & Rohstoffe, Energie- und Rohstoffversorgungstechnik sowie Mining Engineering teil. Schwerpunkt der Exkursion waren lagerstättenspezifische (Steinsalz, Steinkohle, Schiefer) untertägige Abbau- und Gewinnungsverfahren sowie Bergbaumaschinen und -fahrzeuge. Im Rahmen der Exkursion wurden drei Bergbaubetriebe sowie ein Bergbauzulieferbetrieb besucht:
esco european salt company GmbH &Co. KG Steinsalzbergwerk und Saline Borth, Karlstraße 80, 47495 Rheinberg [esco Borth]
RAG AnthrazitI bbenbüren GmbH, Osnabrücker Straße 112, 49477 Ibbenbüren [RAG Ibbenbüren]
Hermann Paus Maschinenfabrik GmbH, Siemensstr. 1-9, 48488 Emsbüren [Paus]
Schiefergruben Magog GmbH & Co. KG, Bad Fredeburg, Alter Bahnhof 9, 57392 Schmallenberg [Magog]
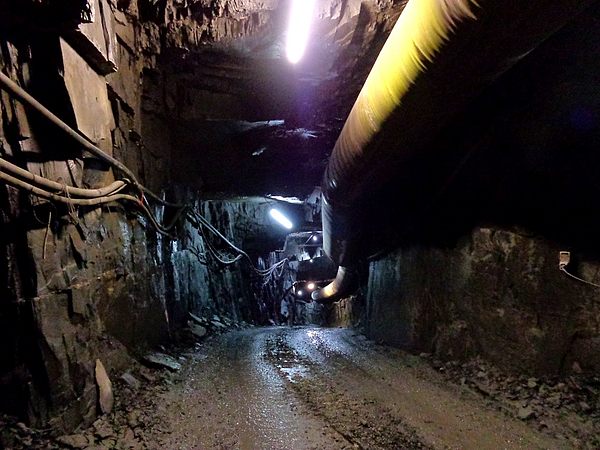
Verlauf der Exkursion
Dienstag, 26.05.2015
| 04:30 Abfahrt in Clausthal 09:00 Befahrung esco Borth 20:00 Übernachtung im Penthouse Backpackers, Osnabrück |
Mittwoch, 27.05.2015
| 08:00 Befahrung RAG Ibbenbüren 15:00 Besichtigung Paus 20:00 Übernachtung im Goalfever Gästehaus, Essen |
Donnerstag, 28.05.2015 | 10:00 Befahrung Magog 16:30 Ankunft in Clausthal |
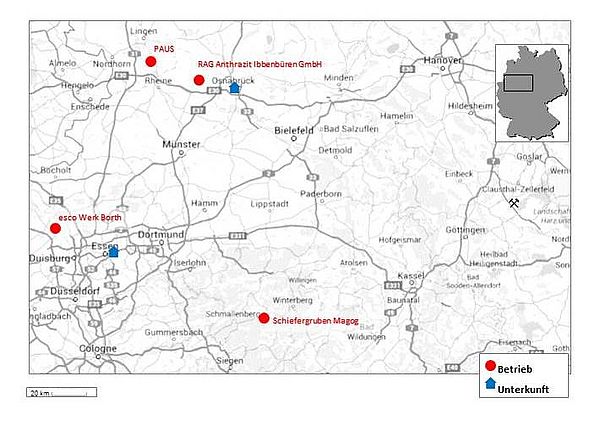
Salzbergwerk Borth der esco european salt company GmbH & Co. KG bei Rheinberg
Das erste Ziel der Bergbauexkursion war das Steinsalzbergwerk der esco european salt company GmbH & Co. KG (esco) in Rheinberg. Nach pünktlicher Abfahrt um 04:30 Uhr in Clausthal-Zellerfeld wurden die Studierenden um 09:00 Uhr freundlich von Grubenwirtschaftsingenieur Nicolai Martens auf Borth empfangen, welcher zunächst einen allgemeinen Überblick über das Unternehmen und die Lagerstätte gab.
Die esco wurde 2002 gemeinsam als Tochterunternehmen der K+S Aktiengesellschaft (alleiniger Besitzer seit 2004) und Solvay GmbH gegründet und ist heute mit einer Produktion von ca. 5 Mio. t Salz (Steinsalz, Siedesalz, Meersalz, Sole) einer der führenden Salzproduzenten Europas. Das Werk Borth befindet sich ca. 30 km nordwestlich von Duisburg und ist neben den Werken Bernburg und Braunschweig-Lüneburg eines von drei deutschen Produktionsstandorten der esco. Mit einer Förderung von ca. 2 Mio t Salz pro Jahr ist das Werk Borth das größte seiner Art in Europa. Auf einer Fläche von ca. 88 km2 wird das Salzvorkommen, welches im Jahre 1897 zufällig bei Probebohrungen nach Kohle entdeckt wurde, seit 1924 in Teufen zwischen 500 bis 1.000 m abgebaut.
Die Lagerstätte befindet sich im südlichen Teil des Niederrheinischen Zechsteinbeckens. Die Entstehung geht auf das Zeitalter des Oberperms (260 – 250 Mio Jahre) zurück, als es durch zyklische Verdunstung des Zechsteinmeers zur Ausfällung mächtiger Evaporitschichten in diesem Gebiet kam. Das ca. 200 m mächtige Borther Salzvorkommen wurde als Teil des Werra-Zyklus abgelagert, wovon heute jedoch nur 20 m der Unteren Werra-Schichten abgebaut werden. Die Salzschichten weisen eine nahezu horizontale Lagerung auf und sind von tonigen Schichtpaketen der Zechsteinfolge überlagert, welche das Salinar vor Wasserzuflüssen schützt.
Das für seine hohe Reinheit bekannte Borther Steinsalz wird heute hauptsächlich als Speisesalz, Futtersalz und Auftausalz für den Winterdienst vertrieben. Des Weiteren findet das Salz in der chemischen Industrie und in pharmazeutischen Produkten Verwendung. Hierbei stellt vor allem die zu Borth gehörende Saline, welche seit 1964 in Betrieb ist und eine Produktionskapazität von bis zu 300.000 t Siedesalz pro Jahr besitzt, ein starkes Standbein des Werkes dar.
Ausgerüstet mit passender Kleidung, PSA und Sauerstoffselbstrettern fuhr die Gruppe anschließend über Schacht Borth II bis auf die Hauptarbeitssohle in 740 m Teufe ein, von welcher das gesamte Streckensystem zum Abbau aufgefahren wurde. Dieser Schacht wird zum Material- und Personentransport genutzt und dient gleichzeitig als einziehender Wetterschacht des Grubenbaus. Der ausziehende Schacht Borth I hingegen dient ausschließlich der Salzförderung und besitzt eine Kapazität von ca. 18.000 t pro Tag.
Nach kurzem Stop in der untertägigen Grubenwarte, welche alle Anlagen und Abläufe des Grubenbetriebs überwacht, fuhr die Exkursionsgruppe mit Herrn Martens und seinem Mitarbeiter mit zwei Fahrzeugen zu verschiedenen Bereichen des Bergwerks, um die Vortriebs- und Gewinnungstechniken und Gewinnungsmaschinen sowie Brecher- und Förderanlagen zu besichtigen.
Die aktuellen Abbaureviere befinden sich in einer Teufe von 800 m - 950 m.Die Länge des gesamten Streckennetzes unter Tage beträgt rund 35 km. Die Streckenauffahrung erfolgt konventionell durch Bohren und Sprengen. Aufgrund der schwankenden Salzmächtigkeiten, hervorgerufen durch ein Graben-Horst-System innerhalb der Lagerstätte, kommen zwei Abbauverfahren im Salzwerk Borth zum Einsatz: Kammerbau mit strossenartigem Verhieb (maximale Kammerhöhe ist 20 m) für Bereiche mit ausreichenden Mächtigkeiten und alternativ der Örterbau für geringmächtigere Abschnitte im Bereich der Horste. Zusätzlich ist die Lagerstätte von einem ausgeprägten Störungssystem durchzogen, weshalb für eine möglichst verlustarme Gewinnung die neuen Abbaue anstatt in Nord-Süd-Richtung in Streichrichtung angelegt werden. Die Salzgewinnung erfolgt durch Bohren und Sprengen, wobei mobile elektrohydraulische Bohrwagen Sprenglöcher herstellen, welche anschließend mit ANC Sprengstoff verfüllt werden. Während des Schichtwechsels erfolgt die Sprengung. Das anfallende Haufwerk wird durch Fahrlader zu den Kippstellen transportiert. Mittels eines Kettenkratzförderer wird das Salz in den Primärbrecher transportiert. Nach der Zerkleinerung wird es auf die Bandanlag aufgegeben, die es zu den schachtnahmen Bunkern transportiert. Mittels Skipförderung wird es anschließend über Schacht Borth I nach Übertage gefördert und weiterverarbeitet. Unter Tage erfolgt nach dem Berauben der Firste die Sicherung mittels eines Ausbaus aus speziellen Spreizanker, welche dem Gebirgsdruck in der aktuellen Abbauteufe besser standhalten als gängige Ankertypen. Ein weiteres Problem hervorgerufen durch den hohen Gebirgsdruck ist die Aufwölbung der Sohlen der aufgefahrenen Strecken innerhalb kurzer Zeiträume und die damit verbundene Verkleinerung der Querschnitte.
Zum Abschluss konnte die Gruppe auch die neu aufgefahrene Flachbunkeranlage in einer Teufe von 740 m besichtigen, die zur Lagerung von bis zu 175.000 t Steinsalz genutzt werden soll, welche die Versorgung mit Streu- bzw. Auftausalz bei erhöhter Nachfrage im Winter gewährleisten soll. Anschließend wurden die Studierenden von Herrn Martens zu einem Mittagsimbiss und abschließender Fragerunde in der Kaue empfangen.
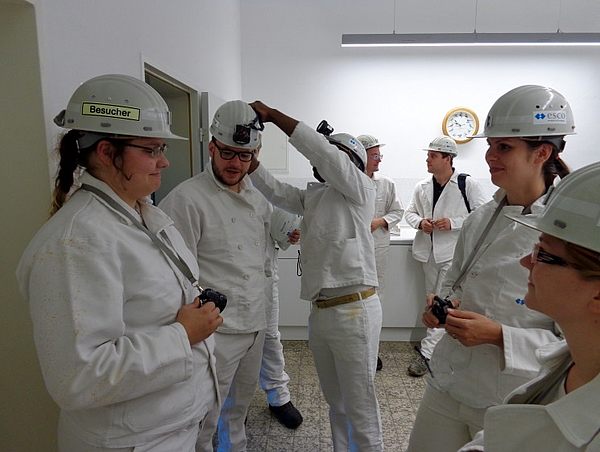
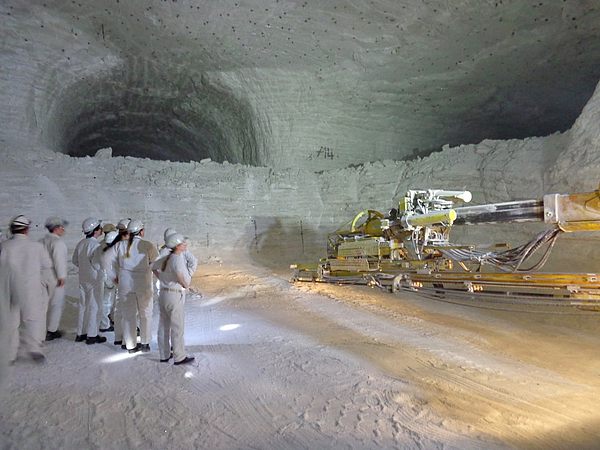
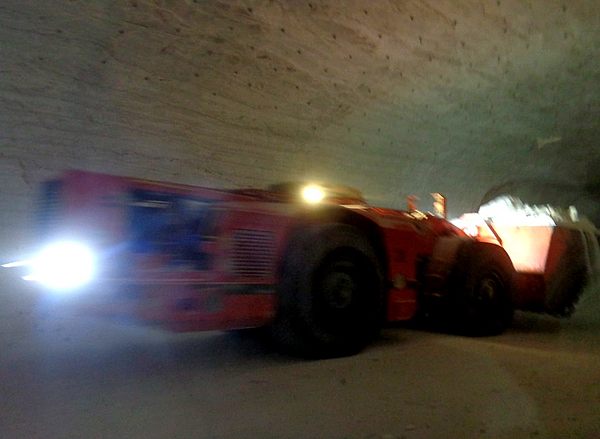
RAG Anthrazit Ibbenbüren
Am Mittwoch stand als erstes eine Befahrung des Steinkohlebergwerks der RAG Ibbenbüren auf dem Plan. Die Exkursionsgruppe wurde im Modellraum zu einem Einführungsgespräch begrüßt.
Die RAG Anthrazit gehört zur RAG Aktiengesellschaft und betreibt eines von drei noch aktiven Steinkohlebergwerken Deutschlands auf dem Gebiet der Stadt Ibbenbüren und der Gemeinde Mettingen. Die Ausdehnung des Grubenfeldes umfasst rund 92 km2 und die Abbauteufen erreichen bis zu 1.600 m, womit Ibbenbüren das tiefste Steinkohlebergwerk Europas ist. Die Förderung beträgt aktuell rund 1,9 Mio t hochwertiger Anthrazitkohle pro Jahr, wird jedoch bis zur geplanten Schließung 2018 schrittweise heruntergefahren werden. Hauptabnehmer ist das benachbarte 840 MW Steinkohlekraftwerk des RWE, während der Rest als Hausbrandkohle unsubventioniert auf dem freien Weltmarkt vertrieben wird.
Das Steinkohlevorkommen von Ibbenbüren ist Teil des nordwesteuropäischen Steinkohlegürtels und entstand zusammen mit dem des Ruhrgebiets im Oberkarbon vor ca. 315 Mio Jahre. Durch spätere Intrusion des Brahmscher Plutons wurde das Richtung Norden abtauchende Ruhrkarbon angehoben und formte den sogenannten Karbonhorst von Ibbenbüren, in dessen Bereich heute die ca. 400 m mächtigen flözführenden Sedimentschichten in relativ geringer Teufe anstehen. Zusätzlich förderte die Hitzewirkung des Plutons sowie hoher Druck die Inkohlung der Flöze, wodurch hochwertige Anthrazitkohle entstand. Die Flözmächtigkeiten schwanken zwischen wenigen Zentimetern und über zwei Metern. Die Ausdehnung der Karbonscholle beträgt ungefähr 14 km in O-W-Richtung und 5 km- 6 km in N-S-Richtung und wird von einer SW-NO streichenden Störung durchzogen, welche die Lagerstätte in ein Westfeld (abgebaut bis 1979) und ein Ostfeld, in welchem aktuell Abbau betrieben wird, unterteilt. Derzeit sind elf abbauwürdige Flöze aufgeschlossen, wobei Flöz 74 mit einer Teufe von bis zu 1525 m den tiefsten Abbaubereich darstellt.
Nach einem Besuch in der Grubenwarte, von welcher aus die gesamte Kohlegewinnung computergestützt gesteuert wird, ging es anschließend weiter zum Umkleiden in die Kaue. Ausgerüstet mit Kleidung, PSA und Selbstrettern begab sich die Gruppe nach Besichtigung der Schachtanlagen auf eine kurze Fahrt zum in der Gemeinde Mettingen gelegenen Nordschacht.
Die Ibbenbürener Steinkohlelagerstätte ist durch ein Streckennetz von rund 90 km und insgesamt sechs Schächte aufgeschlossen: Schacht 3 von Oeynhausen (Hauptförderschacht mit zwei Skipanlagen; 868,5 m Teufe), Nordschacht (Personen- und Materialförderung; 1545 m Teufe), Theodorschacht und Bockradener Schacht (ausziehende Wetterschächte), Schacht von Oeynhausen 1 und 2 (Materialförderung und zeitweise Wasserhaltung). Über den Nordschacht, welcher mit einem vieretagigem Gestell sowie einem Schwerlastkorb ausgestattet ist, fuhr die Gruppe mit einer Geschwindigkeit von 12 m/s in die Steinkohlegrube ein, wo die Einzelheiten der Steinkohlegewinnung vor Ort erläutert und weitere Hinweise zu den Bewetterungs- und Sicherheitsmaßnahmen sowie zu den technischen und geologischen Herausforderungen gegeben wurden. Da zum Zeitpunkt der Befahrung gerade eine Wartung des Kohlehobels stattfand und somit der aktuelle Abbaubereich nicht befahren werden konnte, begab sich die Gruppe zu Fuß zu einem Streb in Raubendstellung. Kriechend bzw. geduckt durften sich die Studierenden durch den rund 1 m hohen Streb bewegen, in welchem nach Entfernung des Hobels gerade die Schilde schrittweise unter zu Bruch werfen des Gebirges ausgebaut wurden.
Der Abbau der Kohle erfolgt durch Strebbruchbau mit schälender Gewinnung mittels eines Hobels. Zur Errichtung der Strebe werden durch Bohr- und Sprengarbeit Kopf- und Fußstrecken parallel im Abstand von 330 m aufgefahren und über Aufhauen verbunden. Die Länge der Abbaufelder kann dabei bis zu 1.500 m und mehr betragen. Zur Sicherung der Strecken wird ein dreiphasiger Ausbau aus Klebeankern in Kombination mit Stahlbogenausbau mit Stahlmattenverzug angebracht, welcher zusätzlich mit Spritzbeton hinterfüllt wird. Die durch den Hobel gewonnene Rohkohle wird über einen Kettenkratzförderer aus dem Streb auf Bandanlagen transportiert und über Zwischenbunker zum Zentralbunker auf die vierte Sohle gefördert. Über den Hauptförderschacht 3 von Oeynhausen, welcher eine Kapazität von bis zu 24.000 t pro Tag besitzt, gelangt die Rohkohle übertage zur Vermischung bzw. Vergleichmäßigung und Aufbereitung. Der Materialtransport unter Tage wird mit Hilfe elektrisch betriebener Einschienenhängebahnen durchgeführt. Die Bewetterung des Grubengebäudes erfolgt saugend, wobei zusätzlich eine Kühlung durch die auf der Schachtanlage Nord installierte Kälteanlage notwendig ist.
Zum Abschluss wurde die Exkursionsgruppe mit einer Bandfahrt zurück zum Nordschacht überrascht und anschließend zu einem reichhaltigen Mittagessen und abschließender Fragerunde in der Kaue empfangen.
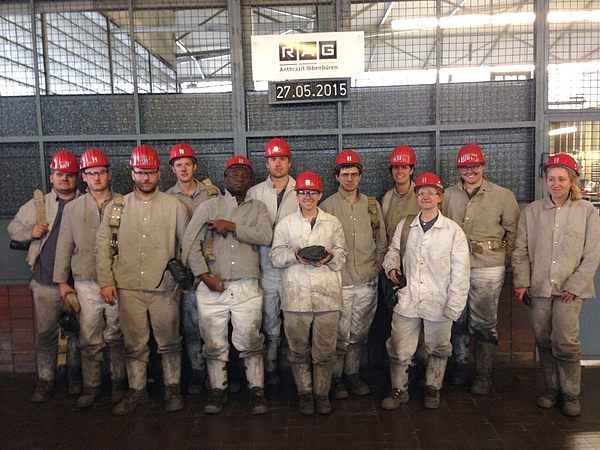
Hermann Paus Maschinenfabrik GmbH, Emsbüren
Am Mittwochnachmittag war die Exkursionsgruppe bei der Hermann Paus Maschinenfabrik GmbH in Emsbüren eingeladen, wo die Studierenden vom Produktionsleiter zu einer interessanten Führung durch die Produktionshallen und Außenlager empfangen wurden. Hierbei wurden betriebsorganisatorische und technische Details erläutert und die zahlreichen Fragen der Studierenden diskutiert. Im Anschluss begrüßte Geschäftsführer Herr Franz-Josef Paus die Gruppe bei Kaffee und Keksen zu einer Präsentation des Unternehmens und anschließender Frage- und Diskussionsrunde.
Die im Jahre 1968 durch Hermann Paus gegründete Maschinenbaufirma ist heute vor allem auf individuelle und kundenorientierte Lösungen spezialisiert und ist mit einer Vertriebsgesellschaft in Chile sowie einer Repräsentanz in Moskau international tätig. Die Produktion der Maschinen erfolgt ausschließlich in Emsbüren, wobei jedes Projekt individuell von kleinen Teams bearbeitet wird. Der Exportanteil durch ein internationales Händlernetz liegt bei rund 70 %, wobei Russland und Südamerika die Hauptabsatzmärkte darstellen. Das Produktportfolio des Unternehmens umfasst u.a. Baumaschinen, Schrägaufzüge, Hubarbeitsbühnen und Krane sowie Berg- und Tunnelbaumaschinen, wie z. B. Fahrlader , Muldenkipper, Berauber, Fahrzeuge zur Streckenerhaltung sowie Vielzweckfahrzeuge. Die Produktion von Berg- und Tunnelbaumaschinen allein beträgt dabei über 60 % der Gesamtproduktion. Für die Studierenden wurde hierbei vor allem deutlich, dass im untertägigen Bergbau oft Speziallösungen gefordert sind, welche den Gegebenheiten und Anforderungen vor Ort angepasst werden müssen um einen effizienten Betrieb zu gewährleisten. Neben der Produktion von Maschinen bietet das Unternehmen auch Dienste wie Wartung- und Reparaturservice, Kundenschulungen sowie ein Austauschteileprogramm an.
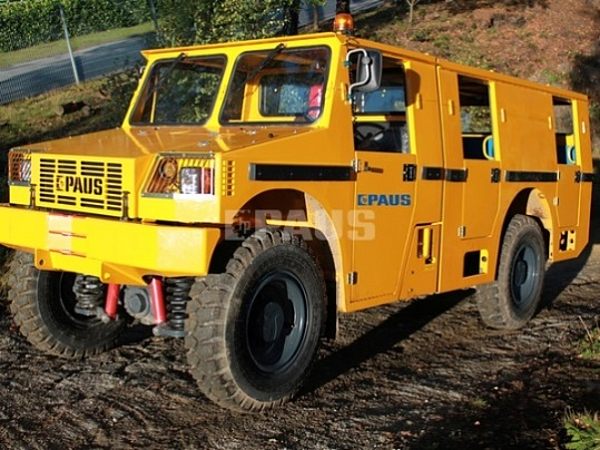
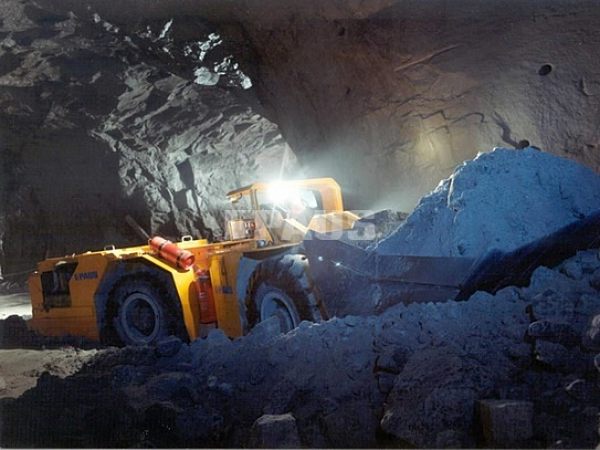
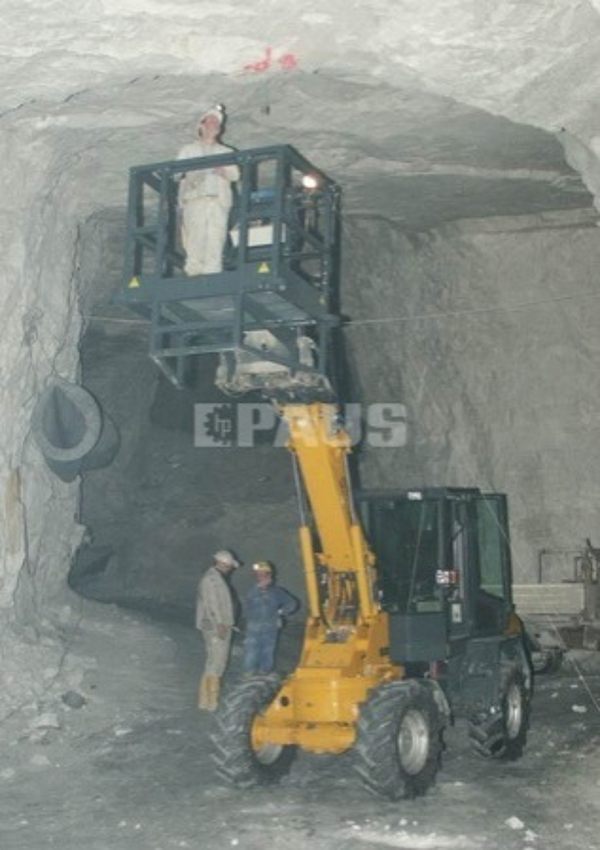
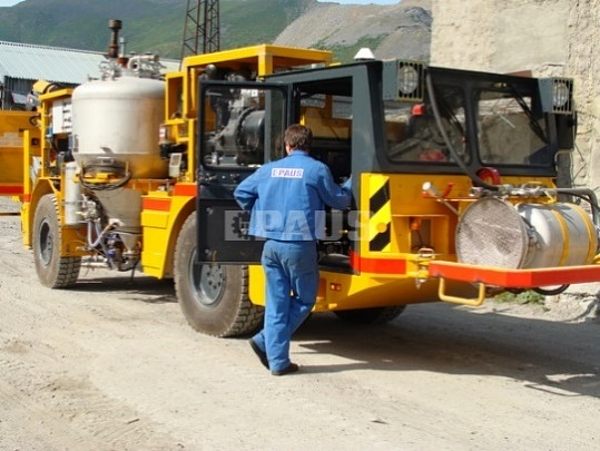
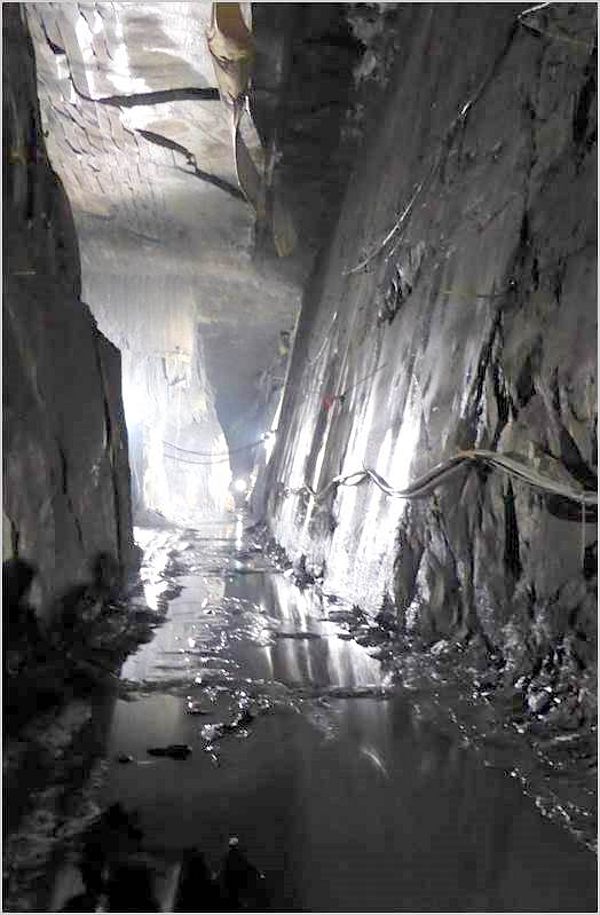
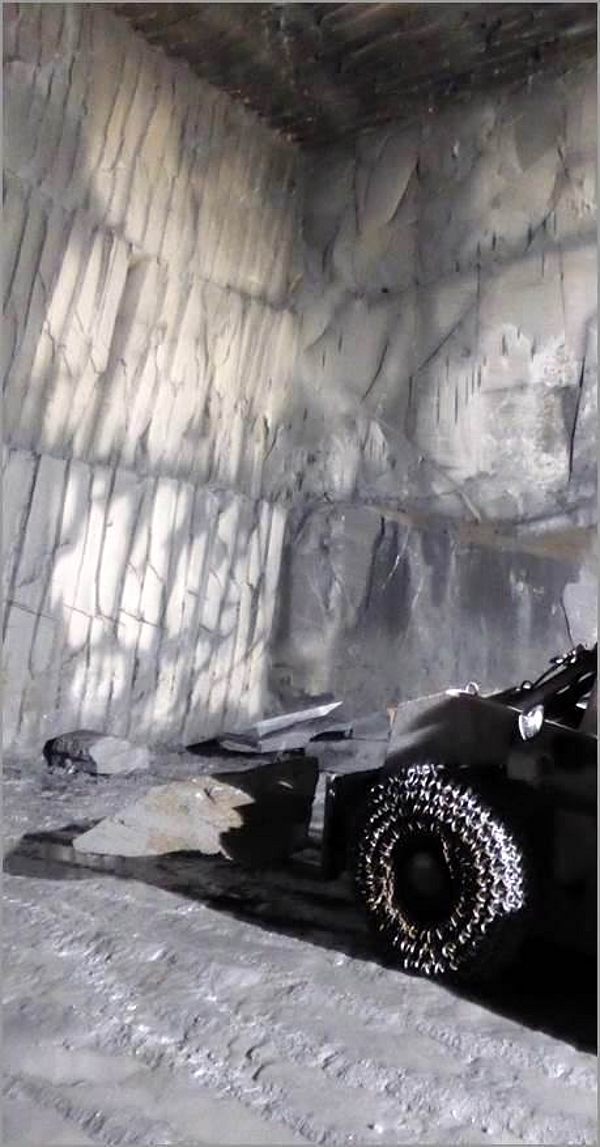
Schiefergruben Magog GmbH & Co. KG, Bad Fredeburg
Für den dritten Tag der Fachexkursion waren die Studierenden zur Besichtigung der Schiefergruben Magog GmbH & Co. KG in Bad Fredeburg/ Schmallenberg eingeladen. Bei einem kleinen Frühstück stellte Betriebsleiter Herr Michael Menn zunächst das Unternehmen vor und führte die Exkursionsgruppe anschließend durch die Produktionsanlagen Über- und Untertage.
Die Grube Magog, welche zum Fredeburger Revier gehört, ist als Teil des Verbundswerks Magog-Gomer-Bierkeller das einzige heute noch aktive Schieferbergwerk von ehemals über 100 Gruben in Nordrhein-Westfalen. Das Schiefervorkommen wurde 1851 durch Zufall beim Ausschachten eines Kühlkellers für eine Brauerei (später Grube Bierkeller) entdeckt und ab 1959 auch in der Grube Magog abgebaut. Heute wird das Gestein von ca. 30 Mitarbeitern in Abbauteufen zwischen 80 m- 120 m gewonnen und in den benachbarten Produktionshallen bearbeitet.
Das im Rothaargebirge gelegene Fredeburger Revier gehört zum Rheinischen Schiefergebirge, in dessen Bereich sich während des Mitteldevons vor ca. 390 - 380 Mio Jahre Tonschichten ablagerten aus denen sich unter dem Einfluss der Gebirgsbildung Schiefer entwickelte. Als Schiefer werden im Allgemeinen Gesteine bezeichnet, welche zusätzlich zur primären Schichtung eine ausgezeichnete Spaltbarkeit entlang engständiger paralleler Flächen (Schieferungsflächen) besitzen, die sekundär durch tektonische Beanspruchung/ Deformation entstanden sind. Durch die im Bereich der Grube Magog erfolgte Überkippung der Tonsteinschichten um 80° und die annähernd parallel einfallende Schieferung ergab sich eine perfekten Spaltbarkeit des Gesteins in sehr dünne und äußerst ebenflächige Platten, wodurch das Schiefervorkommen heute bauwürdig ist und verhältnismäßig einfach nahezu senkrecht gebrochen werden kann. Es erstreckt sich auf einer Länge von ca. 8km und einer Breite von 1 km und zählt zu den größten Schiefervorkommen in Deutschland.
Der Abbau der Lagerstätte erfolgt im Kammerbau, wobei zunächst durch Bohr- und Sprengarbeit eine Strecke aufgefahren wird, von welcher aus in den Abbaukammern (ca. 20 m breit, 5 m hoch) mittels eines Sägegerätes Schieferblöcke von 1 – 2 m2 Größe und 0,5 m Stärke vorgesägt werden. Diese Blöcke werden mit Hilfe eines Hydraulikhammers aus der Wand gelöst und anschließend per Radlader übertage gefördert. Dies geschieht auf drei Strossen pro Sohle, wodurch eindrucksvolle Kammern mit Höhen von bis zu 15 m entstehen. Die Bewetterung erfolgt unterstützt von einer Lutte durch das Mundloch sowie den erst kürzlich angelegten Wetterschacht. Übertage werden die Schieferblöcke anschließend durch eine Sägemaschine zugeschnitten und entweder zu Dachschiefer weiterverarbeitet oder als Naturwerksteinplatten verwendet. Für die Produktion von Dachschiefer werden die zugeschnittenen, rechteckigen Rohblöcke sowohl per Hand als auch computergesteuert in 5 mm starke, rechteckige Schieferplatten gespalten und anschließend durch einen computergesteuerten Roboter oder einen Rechteckautomaten zugeschnitten. Vermarktet wird das dunkelgraue bis schwarze Gestein unter dem Namen „Fredeburger Schiefer“ und kommt hauptsächlich zur Dachdeckung und Fassadenverkleidung sowie als Naturwerkstein beim Innausbau zum Einsatz.
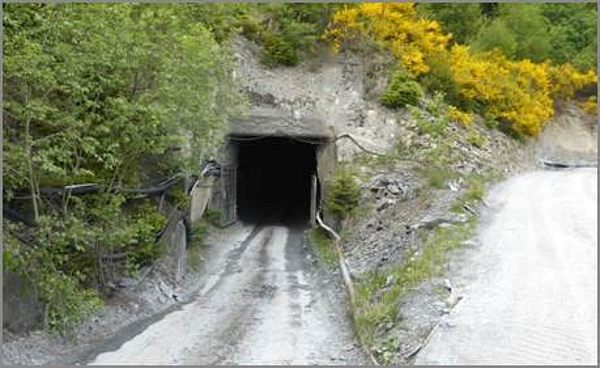
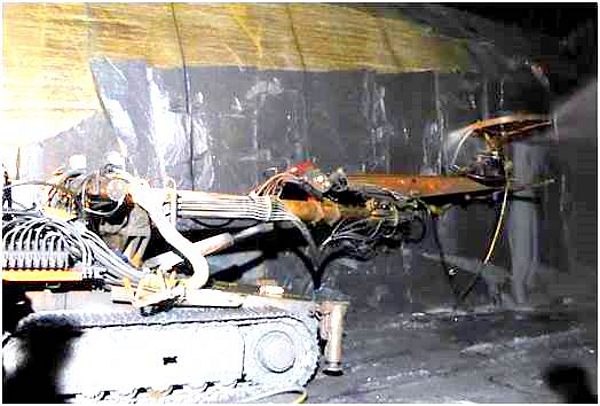
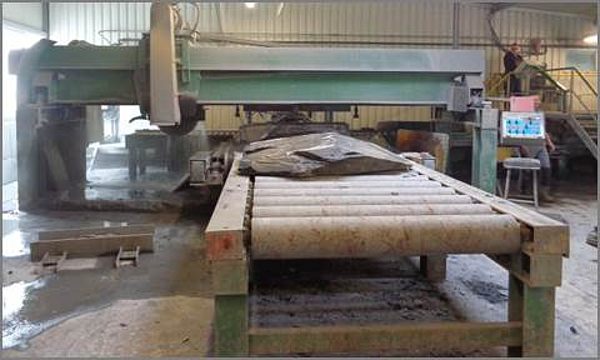
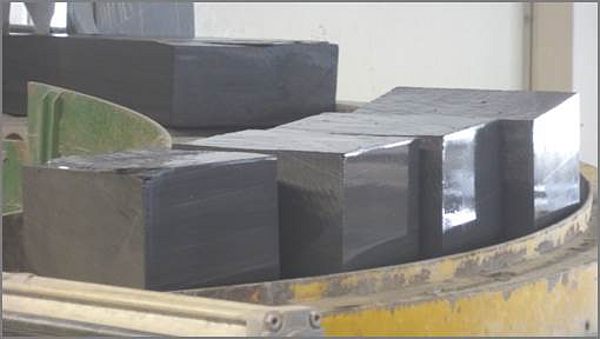
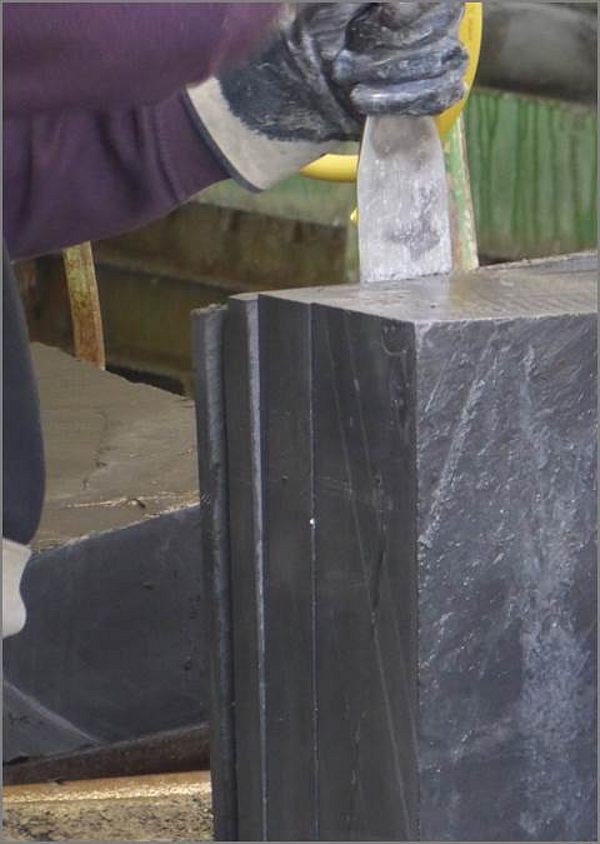
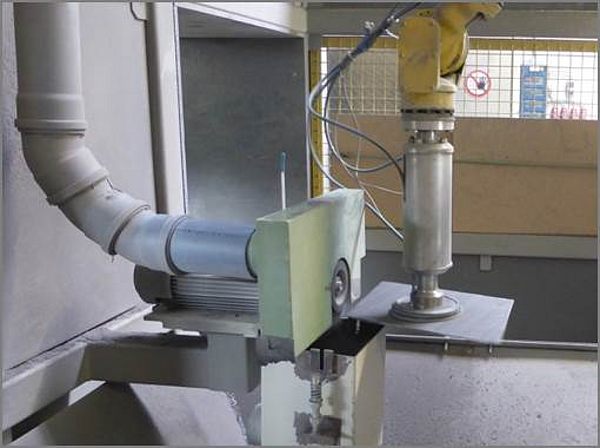
Danksagung
Besonderer Dank gilt an dieser Stelle allen, die diese Fachexkursion unterstützt und zu einem so lehrreichen und aufregenden Erlebnis gemacht haben:
- Institut für Bergbau der TU Clausthal für die Organisation der Fachexkursion.
- esco Borth und Herr Nicolai Martens für die exzellente und umfangreiche Befahrung.
- RAG Ibbenbüren für die einmalige Flözbesichtigung, die wunderbare Betreuung und eine aufregende Bandfahrt.
- Hermann Paus Maschinenfabrik GmbH für den herzlichen Empfang und die umfangreiche und interessante Betriebsführung.
- Schiefergruben Magog GmbH & Co. KG und Herr Michael Menn für eine sehr interessante Führung über- und untertage sowie erfrischende Diskussionen.
- Frau Angela Binder und Frau Stephanie Koschnitzki für die Betreuung der Exkursion und das tapfere Durchhalten auf den langen und frühmorgendlichen Fahrten.
Quellen
Befahrungsmitschriften
Buja, H. O. (2013): Ingenieurhandbuch Bergbautechnik, Lagerstätten und Gewinnungstechnik, Beuth Verlag GmbH, Berlin.
Grabert, H. (1998): Abriß der Geologie von Nordhrein-Westfalen, Schweizerbart'sche Verlags-buchhandlung, Stuttgart.
www.geodienst.de
www.k-plus-s.com
www.magog.de
www.paus.de
www.rag-deutsche-steinkohle.de
www.untertage.com
www.vks-kalisalz.de